Questions and recommendations
FAQs
General
Besides the type (or better, the physical condition) of the medium (liquid or gas) to be filtered, the following filter system information is important: throughput (in m³/h, for instance), operating pressure (in bar, for instance), operating temperature (in °C), medium viscosity or density, solids content or quantity of particles or aerosols to be separated and required filter fineness or separation efficiency.
In process engineering, separation efficiency is the name for the efficiency of the separation process. It is the ratio of material (dust particles, aerosols, etc.) retained by the filter to the unfiltered medium fed into it.
The burst pressure indicates filter element failure when flow is from the inside to the outside. At the burst pressure, the filter element is destroyed and the medium flows through the filter without being filtered. The burst pressure is many times the permissible nominal pressure or operating pressure.
Nominal pressure is the pressure in bar/mbar/kPA for which the filter is designed at room temperature (20 °C).
Service life, or the total duration of filter operation, depends on the contamination level of the medium to be filtered, the required separation efficiency, the filter size and the flow rate.
Viscosity indicates the resistance of a medium to deformation. Generally, the greater the medium's viscosity, the more complex the filter system requirements.
It's simple. Send your application documents with curriculum vitae, photograph and cover letter either for one of the positions we have advertised or unsolicited to karriere@contec-filtration.de
Filter size depends on many factors, including separation efficiency, the desired filter result, duration of use and procurement costs. Contec will be happy to advise you, quickly and competently, considering all necessary parameters.
Consulting for simple filter or fill level solutions is a free Contec service. Consulting for complex systems or filter or fill level solutions that our engineers must design ahead of time will be addressed in an individual offer.
You will receive the filters (filter elements or filter bags) and spare parts directly from us in original Contec quality, quickly and at reasonable conditions. The simplest way is to use our contact form www.contec-filtration.de/en/contact
Unfortunately, we sometimes make mistakes, and given the number of products we offer, things don't always run perfectly in the upstream manufacturing process. If a Contec product does not correspond to the characteristics we guarantee, do not hesitate to contact us. The best thing is to send a detailed description of the fault and, if possible, a photograph of the product in question. We promise to process your issue as quickly as possible and solve your problem to your satisfaction. The e-mail address to use is qualitätssicherung@contec-filtration.de
Gas and air filters
The term "COGA" is protected by the Contec air and gas filtration division. It stands for Contec Gas and Air filters.
Contec adsorbers are used for fine gas cleaning that mechanical filtration cannot manage. An adsorber is a system that consists of an adsorber housing that encloses adsorbents. The adsorbents depend on the elements to be filtered (CO2 or various halogens, for instance).
In addition to drying gases, adsorbers can remove the following:
- carbon dioxide and carbon monoxide
- sulfurous gases
- nitrous gases
- ammonia
- halogens
- heavy-metal composites and metallic mercury
- odorous substances, oil mist, petrol, tar condensate
- toxic and carcinogenic composites
Particle filters separate particles from gases or liquids when the fluid stream is routed into a housing with two connections and through a particle filter element. The filter element flow direction is from outside to inside.
The flow direction in coalescing filter elements is from inside to outside. A coalescing filter element essentially consists of two parts: a coalescing inner layer and a coarser outer layer for discharging the liquid. Aerosols and droplets are captured in the fine fibers of the inner layer, accumulate in the outer filter element layer during passage and move from there to a collection tray.
PTFE is the abbreviation for polytetrafluorethylene. PTFE is a linearly composed polymer made of fluorine and hydrocarbons. The semi-crystalline fluoroplastic exhibits extremely strong bonds between carbon and fluorine atoms. Colloquially, this plastic is often called "Teflon", a DuPont trade name. PTFE is very temperature-resistant.
PTFE's outstanding thermal and chemical resistance make it one of the most versatile plastics in air, gas and liquid filtration. It appears in the Contec filter range in diaphragm filters and candle filters and in the filter housing itself. PFTE is inert and cannot adsorb.
To select the right filter housing and element, consider the following:
- maximum pressure
- maximum/minimum temperature
- chemical and physical characteristics of the filter medium
- filter structure – inlet, particles, coalescence, bypass, diaphragm
- type of contamination
- maximum flow rate
- line diameter and connection type
- required filter fineness
- cost parameters, reaction time, service life and interval
Points 1, 2 and 3 determine the construction material for the filter housing, filter element and seals.
Point 4 is crucial for housing configuration: One connection for intake filters, two connections for inline housings and three connections for coalescing, bypass and fast-loop housings.
Points 5, 6, 7, 8 and 9 determine filter size. This is generally a compromise between factors favoring a small filter (quick reaction time, small space requirements, low cost, minimized adsorption losses) and those favoring a large one (long maintenance intervals, low pressure loss). The decision therefore depends on the importance of these criteria and must be evaluated individually with each application.
Disposable filter elements offer low pressure losses, a long service life and very good filtration characteristics that are harmonized with the medium. It is generally a very economical solution. There is no cleaning and filter elements are replaced 1:1. If the medium is changed, the filter can be adjusted easily and individually to the new medium.
A differential pressure indicator indicates how much of a filter element is "taken up". It can be used to determine when the filter element should be replaced to ensure that the system works without problems and there are no expensive failures.
Oil mist separators
COMS is a registered trademark of the Contec oil mist separator division and stands for Contec Oil Mist Separators.
Contec invented the world's first oil mist separator in 1987. The invention can be credited to engineer Ricard Neuhausen.
Oil mist separators filter oil mist out of the air. Polluted air or a toxic mixture of gases arises when rapidly rotating machine parts are immersed in an oil bath or are constantly wetted with oil for lubrication. This is the case for machines such as wheel gears, gas and steam turbines, turbo engines and compressors used in industry to generate power or compressed air. The oil-gas mixture must be discharged from the machines to prevent oil mist (from the lubricating system) from escaping through the bearings.
Contec oil mist separators essentially consist of a side channel compressor and a filter housing with filter elements. The side channel compressor generates negative pressure to extract the oil-laden air from the lubricating oil tank. The air flows through the intake pipe into the filter housing air distribution panel, where it is distributed to the filter elements and fed through them. The fine oil aerosols in the air are retained in the depths of the filter, collected and finally returned to the machine. The exhaust air thus filtered is, technically speaking, absolutely dry and clean and can remain in the plant without hazard.
Yes, which is why maximum pollution values for emission reduction have been established by law. The values were established in the first general administrative regulation for the German Pollution Control Act (Bundes-Immissionsschutzgesetz) of 27/2/1986 – Technical Instructions on Air Quality Control (Technische Anleitung zur Reinhaltung der Luft or TA Luft). They are governed by the German regulation on large combustion, gas turbine and internal combustion engine plants (Verordnung über Großfeuerungs- Gasturbinen- und Verbrennungsmotoranlagen). This limits the residual oil content of exhaust air to no more than 20 mg per 1 m³ of air, for instance. The emission limits are according to the size and power of the plant in question, the type of fuel and the composition of the gases separated. For many lubricating oils, safety concerns lead to the imposition of a maximum workplace concentration of 5 mg/m³.
Contec oil mist separators can filter oil mist at 99.99% efficiency, eliminating all droplets larger than 0.1 μ. This means that the air discharged into the environment is much cleaner than the German Technical Instructions on Air Quality Control (TA Luft) prescribe. The separators thus fulfill all legal requirements and reliably recapture high-quality lubricating oil, which also usually contains expensive additives. The separated and recovered oil is absolutely clean. It can be fed back through the oil recirculation system into the oil tank without any worries.
The filter elements' long service life and the automatic oil recirculation give the system a low-maintenance design. The longer the system is in operation, the more the filter elements are saturated, including with solid particles. This clogs the pores, increasing the filter's pressure resistance (differential pressure). Filter element condition can be ascertained with a negative pressure gauge. If the COMS filter system is unable to maintain the desired negative pressure in the lubricating oil tank (usually between -10 and -5 mbar), the filter elements should be replaced. The quick-connect fasteners and the swiveling cover (optional) make the filter elements easy to replace. The filter elements are self-sealing and can be easily tightened to the housing with the screw caps on the integrated drawbar.
COMS oil mist separator areas of use range from lubricating oil tanks in gas, steam and water turbines to compressors, gas and diesel engines, vacuum pumps and generators. They are is use in power plants, refineries, LNG terminals and turbine manufacturing plants, for example.
Ultimately, they can, and usually must, be used anywhere rotating machinery is lubricated with oil.
Liquid filter
COLF is the name of Contec's Liquid Measurement division. It stands for Contec Liquid Filters.
Housings made of stainless steel are very resistant to temperature and pressure. If an application involves high pressures and temperatures, Contec stainless steel filters are the go-to solution. The surface can also be treated (polished) so that no germs, bacteria or other microorganisms can adhere to it.
Whenever aggressive media such as acids or lyes are to be cleaned, plastic is the material of choice for filter housings. Contec also offers special filter housings for the chemical and seawater areas.
Meltblown filter candles are manufactured with the meltblown process. Finer and coarser fibers are built up to a multi-layer structures with the finer layers inside and the coarser ones outside. There is a multi-layer gradation. Large particles can be retained in the outer layers and smaller ones in the inner layers.
To create wound filter candles, string is wound around a support (string winding process). Different strings can be used to cover virtually all media, from neutral to aggressive. Wound filters are robust and can absorb lots of contamination (long service life). Other advantages of wound candles are their low differential pressure and high flow capacity.
- pre-filtering in water treatment chemicals
- process filters for solvents
- electroplating
- surface engineering
- oils, greases
- painting and lacquering industry
Activated carbon is a natural product based on natural carbonic raw materials. Its porous structure gives it a very large inner surface, allowing it to bind chemical compounds and molecules.
Activated carbon filters are used to reduce dissolved organic contamination (color, odor, and taste contaminants, chlorine, pesticides and medication residue). For example:
- water treatment
- chlorine separation
- drinking water
- pesticide separation
- pharmaceutical products
- organic material separation
- food and cosmetics
- color and odor removal
Microfiltration is a purely physical separation process. It usually requires no chemical additives. Microfiltration performs separation according to the mechanical size exclusion principle, that is, the filtration principle. For instance, substances in water such as wastewater that are larger than the membrane pores are retained by the diaphragm. Filtration with a diaphragm pore size smaller than 0.1 µm is called ultrafiltration. Filtration with a pore size larger than 0.1 µm is called microfiltration.
Diaphragm filtration is substance separation with filter elements that use porous diaphragms of defined fineness as a filter medium.
A distinction is made between
- microfiltration (pore size about 0.1 – 10µm) and
- ultrafiltration (pore size about 0.001 – 0.1µm)
Separation is largely on the diaphragm surface. The average diaphragm pore size essentially determines the separation effect.
Contec diaphragm filters are always used when high levels of purity for the suspension to be filtered are desired. Contec diaphragm filters can be used most economically when the particle load for the suspension to be filtered is very low. Thus there should be pre-filtering to protect the high-quality diaphragm filter elements from clogging too quickly. Contec would be happy to advise you on these principles.
There are many uses for Contec diaphragm filters. They include the following:
- water treatment (ultra-pure water, demineralized water)
- pharmaceutical products
- food
- beverages (wine, beer, spirits, sparkling wine, mineral water, etc.)
- cosmetics
- high-purity chemicals
- photoresist
- ink
- as a point-of-use filter
The beta value or beta ratio is the proportion of the number of solid particles > x µm before and after filtration.
For example:
- Beta 10 is a separation of 90% of particles of the indicated fineness
- Beta 5000 is a separation of 99.98% of particles of the indicated fineness
Wedge wire filters are also called slot tube filters and are characterized by their simple and fast filtering process Their innovative functionality allows manual or automatic cleaning without interrupting filtration and with minimum product loss during solids discharge.
Contec wedge wire filters can be used with almost all liquids (media), from watery to highly viscous. Examples include the following:
- paints and lacquers
- emulsion paints
- printing inks
underseal - tar products
- cooling lubricant
- adhesives
- solvents
- transmission oil, rolling oil, rapeseed oil
- emulsions
electrophoresis lacquer - chocolate mass
- yeast
- plasticizers
polyurethane
Filtration goes from the outside of the filter element to the inside, with the solids accumulating on the outside. Cleaning proceeds as follows: The geared motor turns the cylindrical filter element. Particles that are larger than the slot in the filter element accumulate on the surface and are scraped off by a blade. The solids collect in the bottom of the filter housing (filter sump), where they can be removed manually or released automatically and disposed of.
Contec filter bags are used to filter solids from liquids in such applications as water treatment, the electronics and photography industries, chemicals, surface engineering etc. Filter bags are made of a variety of materials and are easy to harmonize with a specific medium and filtration degree. Filter bags are an economical filtration solution.
Fill level measurement
Contec Liquid Measurement, a Contec division.
A capacitive sensor is based on changes to an alternating electric field. A liquid's fill level, in a tank, for instance, influences the strength of the alternating field that the sensor generates. The sensor uses this change in electric capacity as a measuring signal.
For fill level measurement with a capacitive fill level sensor, exact information about the liquid is needed ahead of time. Sensor precision depends on the dielectricity constants of the medium to be measured. If the liquids or fuels are to change (diesel or biodiesel, for instance), Contec offers special solutions such as sensors with manual or automatic calibration.
Typical application areas for capacitive fill level sensors are tanks of motor sport vehicles, utility vehicles and agricultural and construction machinery and in mobile tanks. Capacitive sensors can measure liquids such as coolant, lubricant, fuel and motor and hydraulic oil.
Mechanical fill level indicators can be observed and evaluated in a fraction of a second, much like a clock face, where the position of the hands is enough to tell the time. Fill level indicators are simple and robust in design and can easily be adapted to individual tank dimensions, sometimes by simply shortening them. They require no power connection. Contec fill level indicators can also be retrofitted with an addition signal output with a Twinsites indicator face.
Fill levels in a tank can be measured by such means as electrically capacitive, radar-guided or mechanical equipment. The COLM product range also includes level switches for detecting when a liquid is at a certain level.
The most commonly used Contec sensors are capacitive and electromechanical sensors. Fill levels can also be monitored optically, hydrostatically or with ultrasound.
Contec fill level sensors can be used in many ways. For example, they detect the fill levels of liquids in reservoirs and storage tanks. They also monitor critical process states in such situations as when a hydraulic tank is emptied or the inadvertent overfilling of a tank must be prevented.
Other possible uses include the following:
- monitoring oil fill levels in machine and plant engineering
- measuring the fill level of cleaning fluid and cooling lubricant
- preventing inadvertent overfilling/emptying of open and closed containers, hydraulic tanks, silos and storage tanks
If only one level or switching function (such as a maximum or minimum warning signal) is needed, the COLM fill level switch is the right mechanism. The switches are used classically to monitor pumps or record warning signals when liquid falls below a certain level.
We are here for you: contact persons at a glance
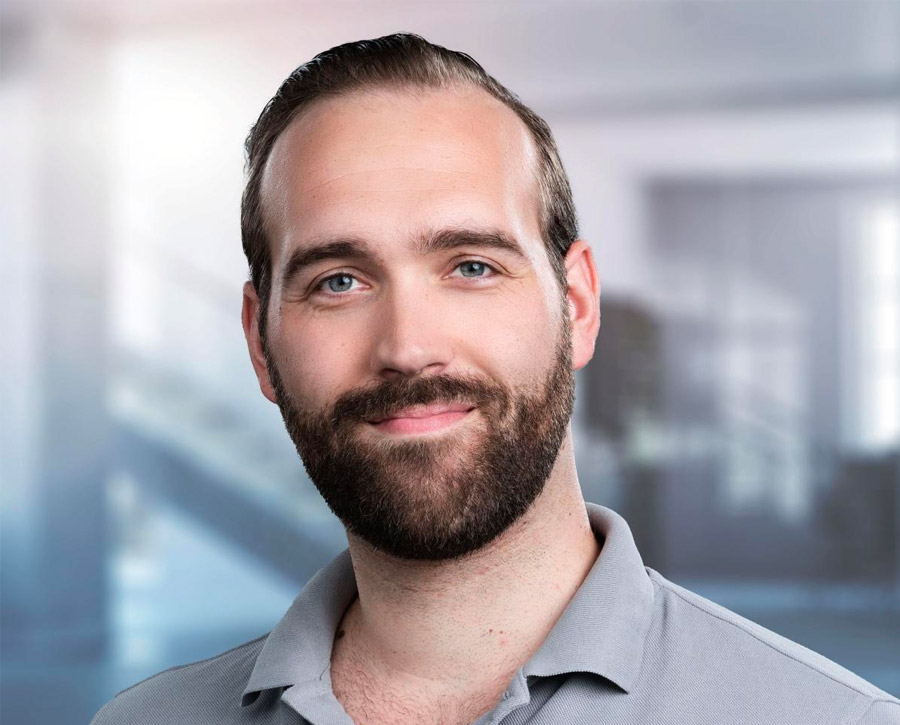
Air and gas filters (COGA)
Air and gas filters (COGA)
Marcel Muß
Internal sales
+49 (0)2224 9893-27
muss[a]contec-filtration.de
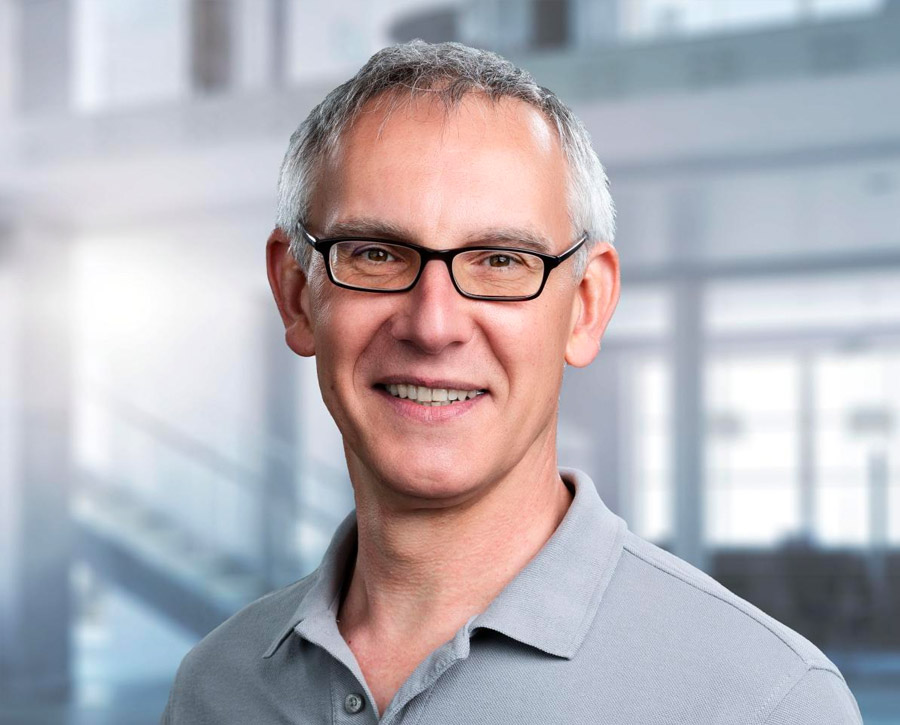
Oil Mist Filtration (COMS)
Oil Mist Filtration (COMS)
Frank Ketteniss
Product Manager
+49 (0)2224 9893-12
ketteniss@contec-filtration.de
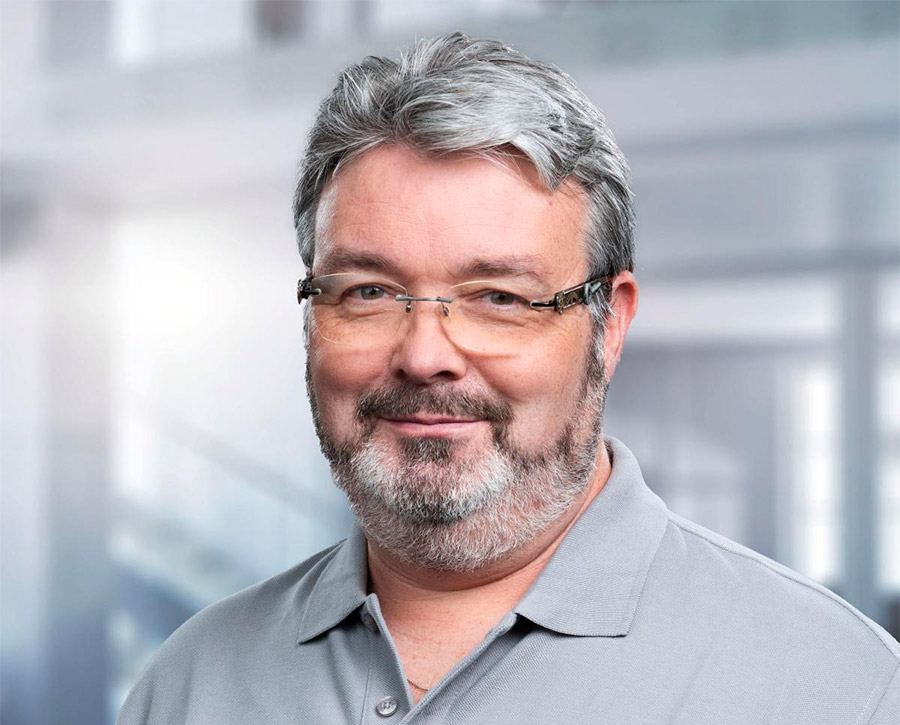
Liquid filters (COLF)
Liquid filters (COLF)
Helmut Scherer
Product Manager
+49 (0)2224 9893-18
scherer[a]contec-filtration.de
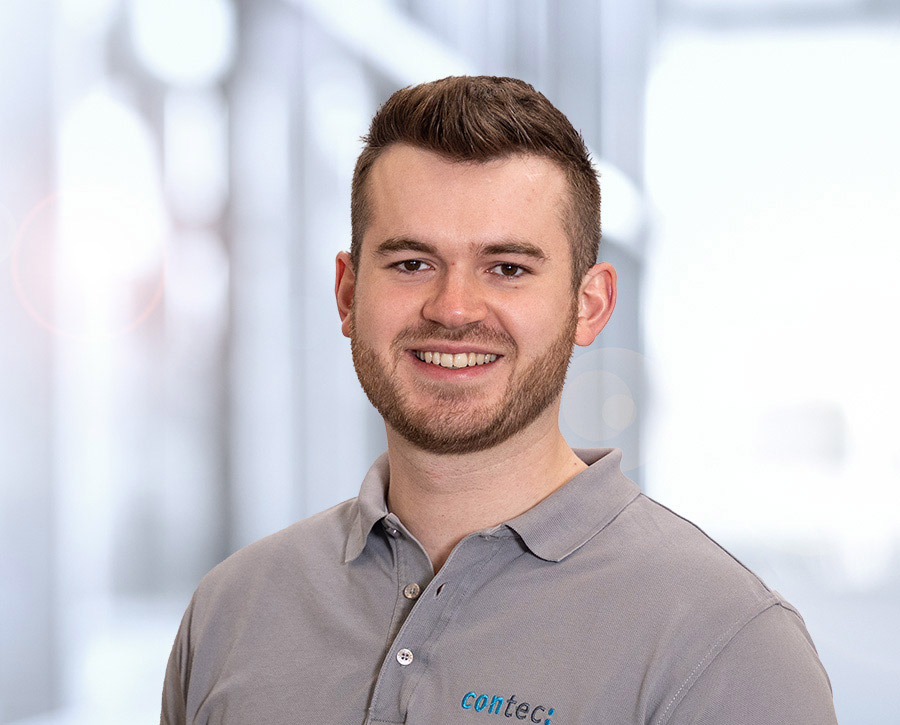
Level measurement (COLM)
Level measurement (COLM)
Jannik Joest
Internal sales
+49 (0)2224 9893-11
joest[a]contec-filtration.de